Advances in Divider Blocks
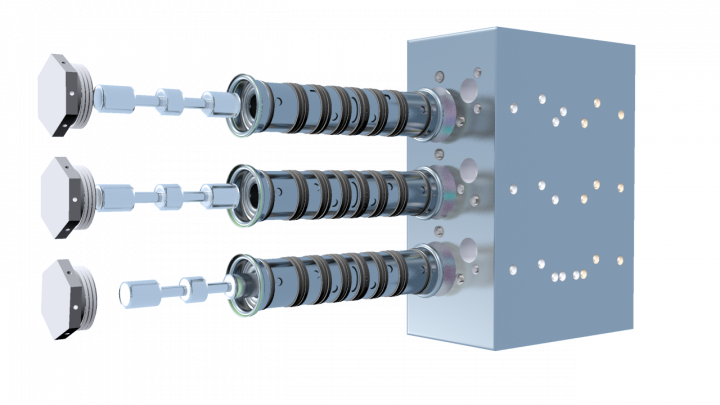
Current divider block designs are potentially the most troublesome part of a lubrication system.
Replacement blocks are relatively expensive. They take significant time to change which not only costs in labor, but also in lost compressor run time. The O-rings required maintaining the high pressure seals can get lost or damaged leading to costly leaks and performance issues. The process of torqueing the mounting bolts can lead to deformations of the piston requiring another replacement.
All of these issues will come up whether the block needs to be replaced due to long term wear, damage from particulates in the lubricant, or you need to change the size of the pistons to match changes in operating conditions.
If you were offered a solution to these issues and it was less expensive than the current design solutions, would you be interested?
The one piece Transformer “Mono Block” series of divider valves solves all existing divider block issues and does so at a cost that that is lower than current designs and they last longer!
The ground-breaking change in design of the Mono Block is the way pistons and cylinders are implemented. Instead of the bore of the divider block serving as the cylinder, the Mono Block uses a swappable precision steel cylinder inserted in the block. The added strength of the steel means the block will last much longer and is nearly impervious to stress strains associated with over torque of the mounting bolts. The porting in the cylinder is easily accessed in the manufacturing process which translates to reduced costs. Compression seals maintain the isolation between ports and allow the cylinder to be easily installed or removed. The overall block can be made from a number of materials that match the intended environment. When composites are used, the costs are significantly reduced. The pistons are precision ground and fit to the cylinder with less than 8 millionths of an inch tolerance.
The cylinders are completely swappable by removing the end plugs and pushing the cylinder out. A new cylinder - piston pair is inserted and the reconfiguration is complete. No disassembly of the blocks is required. The entire operation can be completed in a couple of minutes, not the hours traditional designs require and no special tools or skills are needed.
Mounting plate adapters allow the Mono Block to easily mount to compressors with exactly the same mounting bolt pattern as industry standard blocks.
The one piece design eliminates the problems associated with the O-rings located between sections because they are no longer required.
The one piece Mono Block is easily stocked in 6, 8, 10 and 12 outlet configurations. These 4 basic parts are quickly configured with any of the wide selection of cylinder - piston pairs. Suppliers can have a complete divider block assembly built to customer specs in minutes, not hours. The overall effect is a reduced inventory cost with the same amount of product availability and much shorter assembly times.
The Pro Series of divider blocks are designed to replace a standard design block in a current installation. You can incrementally upgrade to the newer design one block at a time.
The Mono Block and Pro Series Divider blocks are less expensive, more reliable, more durable, easier to change, and less hassle to stock and configure than traditional blocks. The question shouldn't be whether to use these divider blocks, the question should be why haven't you already?